Release of version 5.7
New developments and optimizations for FUTURA Engineering | July 2025
📢 New developments for version 5.7
Item list
Extension for the use of factor values for price components
With the current release, the price component function has been expanded for both buyers and suppliers. The aim of this further development is to enable the supplier to apply factor values to the predefined prices per price component as part of the quotation process. This enables a flexible adjustment of the price structure on the basis of individual calculation approaches. All the new features are summarized in detail below:
Adoption of predefined prices with price components in item lists
Since version 5.6, it has been possible to manage price components in item lists. FUTURA Engineering now also supports specifications with default prices per price component. In order to meet the specific requirements – in particular the requirement that suppliers are not allowed to change the predefined prices per price component, but can apply a uniform factor per price component across all service lines, the following new option for request has been introduced:
Default prices with price components and factors as well as price request
The new option in the tab "Header data" allows:
The predefined application of factors to fixed predefined prices per price component
The secure execution of a price request without suppliers being able to change the specified price components
A simplified and structured recording of the factors per price component, which are then automatically applied to all service lines in the quotation
Exception: The factor does not apply to service lines for which the customer does not specify any default prices in the item list (e.g. for hourly wage work). In these cases, the supplier enters the unit price itself as usual.
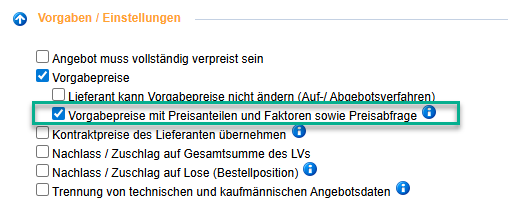
For more information, see the help article:
Default prices with price components and factors and Price query
Master item list
Support of price components
As an additional extension to the previous point, the master item list has been extended to systematically support stored service lines with assigned price components. This allows price component structures to be maintained sustainably and transferred to follow-up processes.
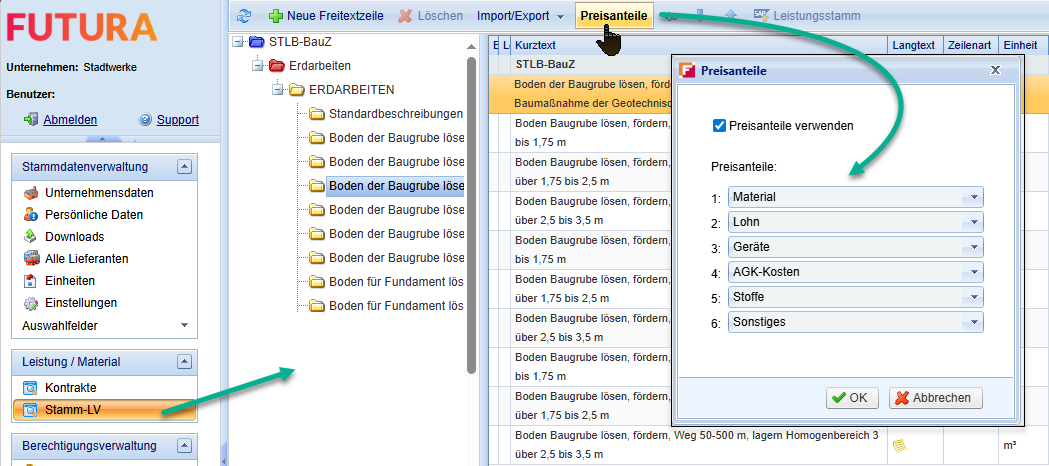
Short description
Formattable text for short descriptions
For this version 5.7, the short description field in Requests and Purchase Orders has been fundamentally revised and expanded. With this implementation, you can use a formattable input of the short description, which ensures better readability and structured presentation for your suppliers. This also applies to internal users who have insight into their processes in FUTURA Engineering. The formatted text is displayed in this form in the invitation to the suppliers.
SAP integration
As before, the short description is transferred to SAP as plain text. HTML formatting is not taken into account.
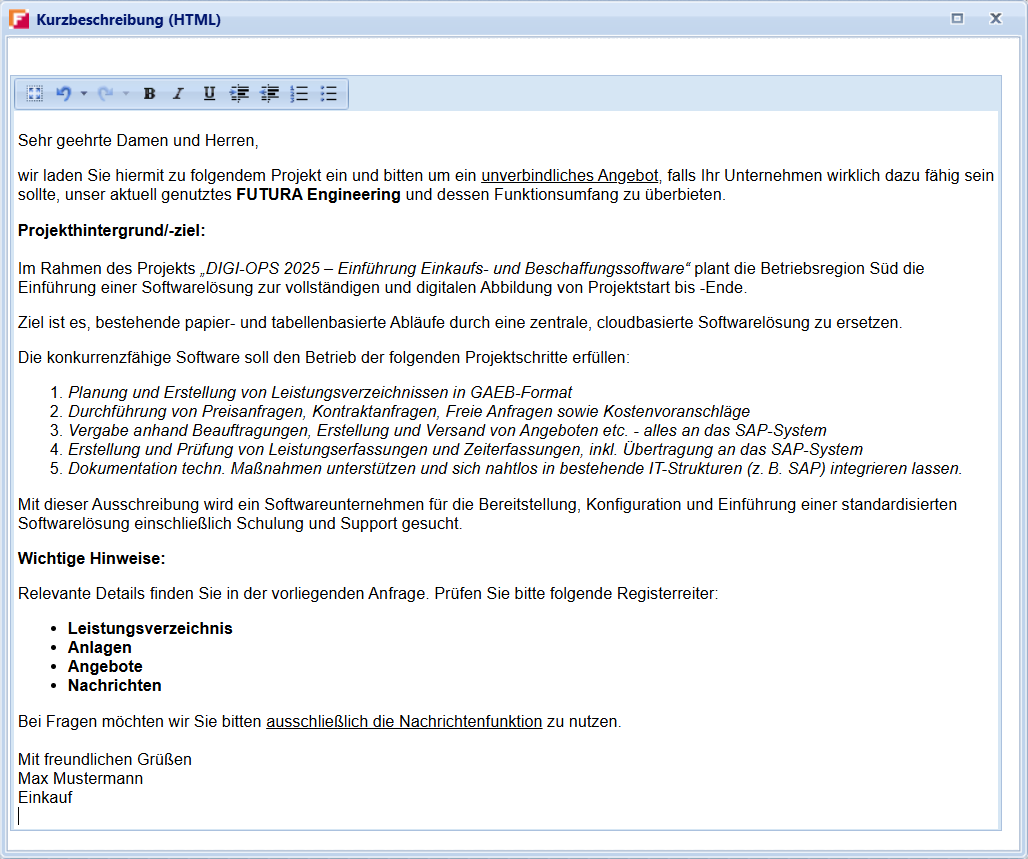
Specifications
for the layout function in the course
With this enhancement, the function to show and hide columns as well as to save individual layouts is now also available in the individual processes for editing item lists. This means that you can now use the following in the modules Requisition, Request and Order:
Flexibly show and hide columns
Save and reuse custom layouts
This function has also been made possible for suppliers in the quotation creation process, so that the individual adaptation of the view depending on the work focus makes work easier for both sides.
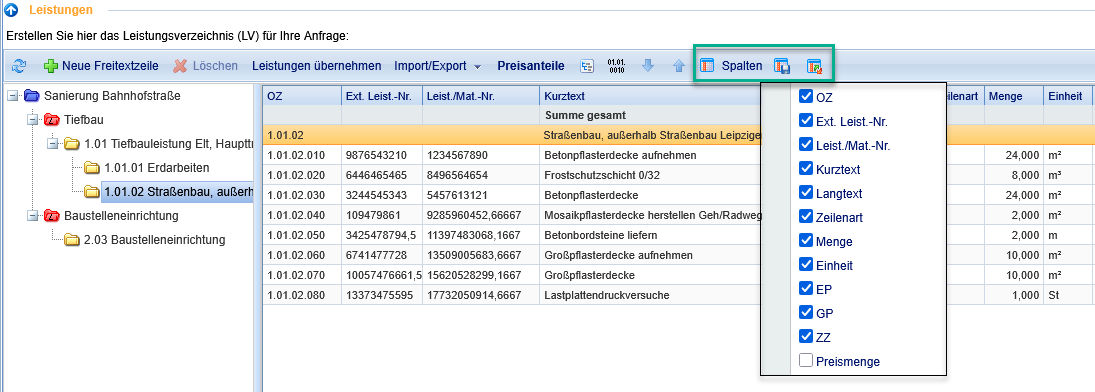
Requests
Status Visualization
For a better overview in the request process, the request list has been supplemented by an extended status display. The status display is based on the familiar logic from request evaluation.
The overview for requests now shows the processing status per supplier. The following statuses are available:
Not viewed: The request has not yet been opened by the supplier.
Viewed: The request has been opened, but there is no response yet.
Rejected: The supplier actively rejected the request.
Accepted: Participation has been confirmed (an quotation is awaited)
Submitted: The supplier has submitted a quotation.
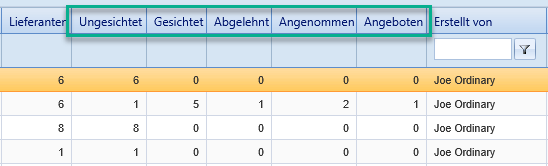
Item list
Optimization of the check filter for item lists in all modules
With this release, the previous check protocol button is replaced by the new and optimized check filter function. This improves the quality assurance of item lists through automated test criteria directly in the work process and reduces the workload.
The check filter is available for all areas where you can create a item lists. This applies to the following types of transactions:
Requisition
Request
Order
Order Change Management
How the Check Filter works
By clicking on the new Check Filter button, a settings window opens in which various test criteria can be individually selected and combined. After applying the filters, the results are displayed directly in the item list view.
Available test criteria:
Account assignment is missing (already existing – integrated into the new window)
The quantity of a service line is 0
Unit Price is 0
After selecting and applying the filter criteria, the item list is displayed filtered accordingly. For a better overview, use the Hide Tree function to show all affected service lines one below the other.
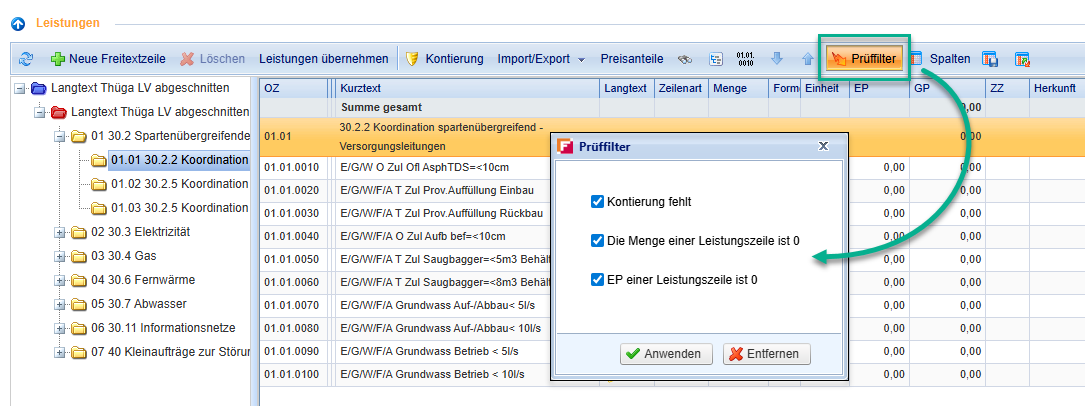
System mails
New infomail at every start of a request
As additional information, an info mail is now automatically sent to the responsible commercial contact person and his representative when an request is started. This e-mail contains an overview of all supplier companies, including the e-mail addresses used for the contact persons who were contacted in the current round of the request.
The infomail is sent again every time a new round of a request is started. Especially when new suppliers have been added to the request.
Infomail is triggered in the following cases:
the first publication of the request
the start of a new quotation round
Adding new suppliers to an ongoing request
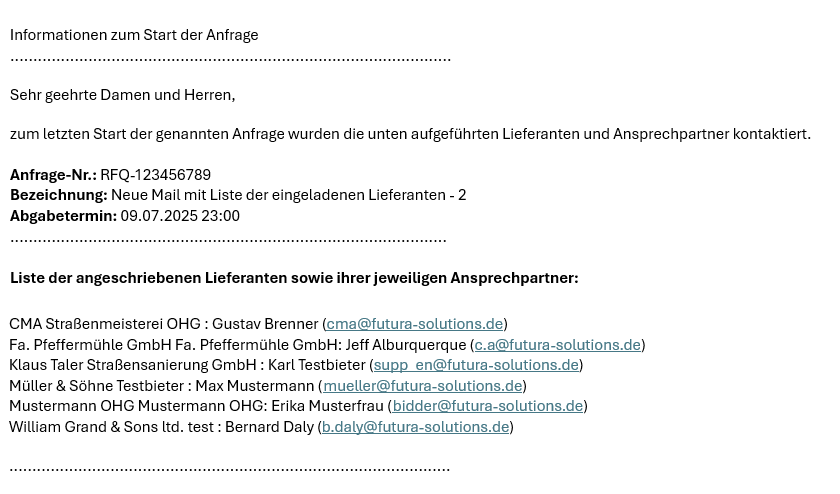
Message function
New information on the processing status
The message function for requests has been expanded to include the new column "Processing status supplier". You can now view the current processing status of the same in the dialog box for selecting suppliers, which makes tracking and communication much easier.
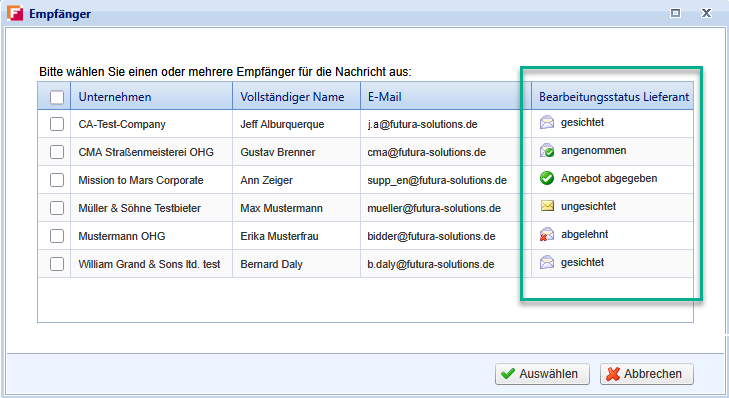
Time Tracking
Optimization of Time Tracking
Recording of working hours via performance recording by means of time recording
In FUTURA Engineering, it is already possible to enable your service providers to record working hours for orders in addition to service recording. These can document the specific work period (including date, time and from/to times) as well as a job description in appropriately configured service lines.
Surcharges for overtime, night or holiday work are automatically calculated based on company-specific surcharge tables previously created by the supplier. The working hours recorded by the supplier are automatically compared with the data from your SAP time recording system for verification.
New in version 5.7: Time tracking also possible without an SAP connection:
From version 5.7 onwards, this function can also be used if no time recording is carried out in SAP – e.g. on construction sites or in smaller plants/offices without card readers for external service providers. In this case, time recording is carried out exclusively by the supplier in FUTURA Engineering and is used by you for review and approval. After your approval, the service entry sheet is generated in SAP as usual.
The following further developments have been carried out in time recording:
Enhancement 1: Enhancement for Transferring Services from Ordering Orders (SAP)
When transferring services from orders (= orders from SAP), it is now possible to also transfer time recording service lines. This facilitates and automates the continuous documentation of time-related services.
Extension 2: Use of time recording even without an SAP time recording interface
The existing SAP interface for retrieving time recording data can be optionally deactivated. This enables the supplier to define the required working time in the activity entry for service lines with defined time recording units (e.g. hours). On the auditor side, the audit is carried out without time recording in SAP. This allows the exclusive use of the internal system for time recording.
Enhancement 3: Revision of the review window for time tracking data
The window for checking time tracking data has been comprehensively revised. The display has been optimized to facilitate predefined tracking and correction of time entries.
Extension 4: Detailed information in the time recording window
For better traceability in the Time Tracking window, the following information is now provided:
Order number
Registration number
Reference number / external service number
Service or material number
This information increases transparency and data quality in the recording and auditing of time-related services.
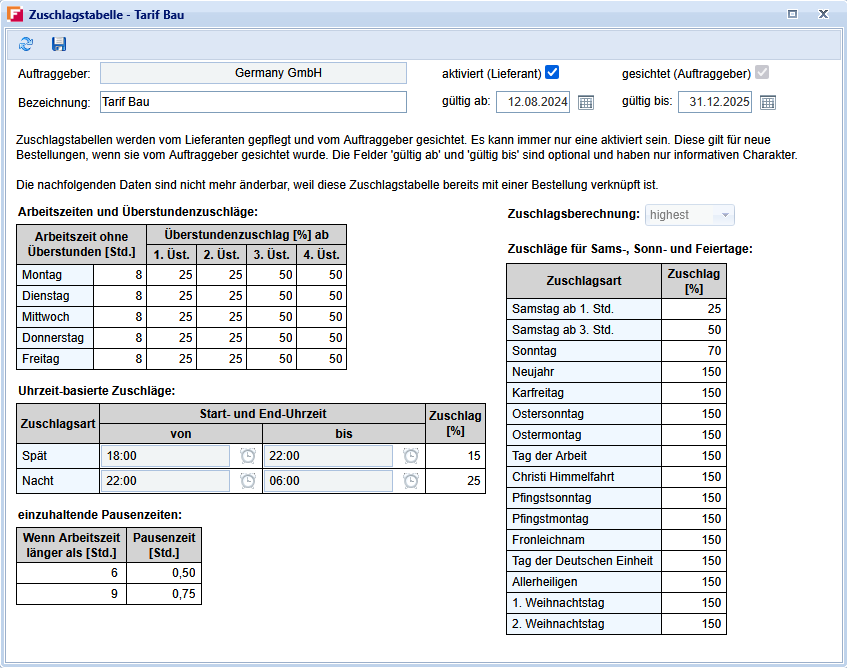